Things about Oems
Wiki Article
The Best Strategy To Use For Lean Production
Table of ContentsSome Known Questions About Lean Production.Manufacturing Industries Fundamentals ExplainedUnknown Facts About Plastic ManufacturingGet This Report on Lean ProductionThe smart Trick of Die Casting That Nobody is Talking AboutThe 15-Second Trick For Lean Manufacturing
The text on this web page is a sample from our complete White Paper 'Shot Moulding for Buyers' - * Sample message * - for complete overview click the download switch above! Intro This overview is planned for individuals that are looking to source plastic mouldings. It offers a much required understanding into all that is involved with developing plastic components, from the mould tool called for to the moulding procedure itself.If you wish to check out better, the overview covers sorts of mould devices, along with special completing procedures such as colours & plating. Words that are highlighted can be located in the reference in the appendix ... Component I: Moulding: The Essentials The Benefits of Shot Moulding Plastic shot moulding is a really specific procedure that offers a number of advantages over other plastic processing approaches.
Precision is ideal for really detailed parts. Contrasted to other techniques, moulding enables you to integrate more features at really small resistances. Look at the picture to the right. mfg. You can hold this moulding in the palm of your hand as well as it has bosses, ribs, metal inserts, side cores and openings, made with a moving shut down function in the mould tool.
10 Simple Techniques For Mfg

from material feed & melting; material injection; shot time cooling down ejection as well as the re-closing of the mould tool ready device the next cycle. Draft angles - The wall surfaces of a moulded component should be somewhat tapered in the instructions in which the part is expelled from the mould device, to allow the component to be ejected quickly.
Ejector stroke - The pushing out of ejector pins to expel the moulded part from the mould tool. Ejector stroke rate, size and also timing requires to be very carefully regulated to avoid damage to the ejectors and also mould device, however at the very same time make the moulding cycle as brief as feasible.
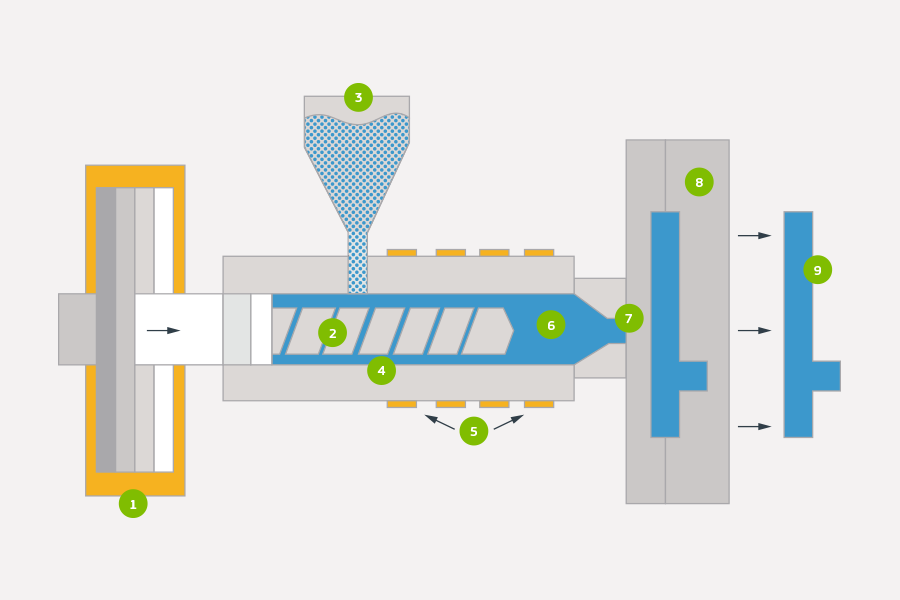
8 Simple Techniques For Oem
Ribs - When a plastic part has slim wall surfaces, ribs are contributed to the style to make the slim walls stronger Side cores - Side action which generates a feature on a moulded component, at an opposing angle to the normal opening instructions of the mould device. additive manufacturing. The side core needs to be able to retract as the plastic part can not be ejected otherwise.
Wall surfaces - The sides of a moulded component The message on this page is an example from our full White Paper 'Injection Moulding for Customers'.
Production process for generating components by injecting molten material into a mould, or mold Streamlined representation of the procedure Injection moulding (U.S. spelling: shot molding) is a production process for creating components Clicking Here by infusing liquified material right into a mould, or mold. Shot moulding can be performed with a host of materials mostly including metals (for which the process is called die-casting), glasses, elastomers, confections, and also the majority of typically thermoplastic and thermosetting polymers. Injection moulding is commonly made use of for making a range of components, from the tiniest elements to entire body panels of cars. Developments in 3D printing innovation, using photopolymers that do not thaw during the injection moulding of some lower-temperature thermoplastics, can be made use of for some basic shot moulds. Injection moulding uses a special-purpose maker that has three components: the injection device, the mould as well as the clamp.
The Ultimate Guide To Mfg
, with the quantity utilized of the previous being substantially higher.: 13 Thermoplastics contract manufacturing are prevalent due to characteristics that make them highly appropriate for injection moulding, such as simplicity of recycling, adaptability for a wide variety of applications,: 89 as well as capacity to soften and move on home heating.In several tooth cavity moulds, each tooth cavity can be identical and develop the very same parts or can be distinct and develop several different geometries throughout a single cycle.
The screw provides the raw product onward, blends and also homogenises the thermal and viscous distributions visit their website of the polymer, and decreases the needed heating time by mechanically shearing the material and adding a substantial amount of frictional home heating to the polymer. The product feeds onward through a check shutoff and collects at the front of the screw right into a volume understood as a shot. When enough material has actually collected, the material is forced at high pressure and speed into the part forming cavity. The exact quantity of shrinkage is a feature of the resin being used, and can be reasonably foreseeable. To prevent spikes in pressure, the procedure generally uses a transfer position corresponding to a 9598% full dental caries where the screw shifts from a constant speed to a continuous stress control.
Some Known Factual Statements About Hon Hai Precision
As soon as the screw reaches the transfer position the packaging stress is used, which finishes mould dental filling as well as makes up for thermal shrinking, which is rather high for thermoplastics about lots of other materials. The packaging stress is applied till the gateway (dental caries entry) strengthens. As a result of its little dimension, eviction is typically the initial location to strengthen through its entire thickness.: 16 Once the entrance solidifies, say goodbye to product can enter the tooth cavity; accordingly, the screw reciprocates and acquires product for the following cycle while the product within the mould cools down to make sure that it can be expelled and be dimensionally stable.Report this wiki page